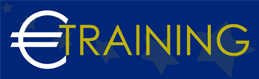

Pipes and Piping Systems Optimization
Overview:
Introduction:
Optimizing pipes and piping systems is essential for enhancing the efficiency and reliability of fluid transport in industrial operations. This process involves designing, selecting, and maintaining piping networks to minimize energy loss, reduce costs, and ensure safe, smooth flow. This training program provides comprehensive instruction on enhancing the efficiency and performance of piping systems in various industrial applications.Through it, participants will gain the knowledge and skills necessary to design, analyze, and manage piping systems effectively, improving overall system reliability and productivity.
Program Objectives:
At the end of this program, the participants will be able to:
-
Explore various piping system types, their classification, and design standards.
-
Calculate pressure losses, velocity distribution, and select appropriate pipe sizes for different fluids.
-
Evaluate pump and compressor interactions within pipelines and apply selection criteria for multi-pump/compressor stations.
-
Select and size control valves, analyze cavitation issues, and understand automation control for pipelines.
-
Implement operation and maintenance strategies, including leak detection, corrosion prevention, and pipeline safety measures.
Targeted Audience:
-
Plant professionals dealing with operation pipeline systems.
-
Engineers responsible for the reliability of operation.
-
Engineers and technical staff in charge of inspection and condition monitoring.
-
Technical professionals involved in technical support and maintenance and repair.
-
Engineers in charge of the planning of new pipelines and retrofitting old ones.
Program Outlines:
Unit 1:
Overview of Piping Systems:
-
Main features of various types of piping systems.
-
Classification of piping systems based on the design and application.
-
World standards and codes on design properties of pipes.
-
Main steps in the design and construction of piping systems.
-
Physical and transport properties of fluids: density, viscosity, particle contents.
-
Basics of flow analysis in pipes - laminar and turbulent flow regimes.
Unit 2:
Calculation of Pressure and Velocity Distribution in Piping Systems:
-
Calculation of pressure losses and horsepower required for fluid transportation.
-
Selection and sizing of pipes for different applications: liquids, gases, slurries.
-
Calculation of minor losses in the piping system.
-
Basics of mechanical design: a selection of pressure class of pipe and stress ratios.
-
Hydrostatic testing: allowable operating pressure and hydrostatic test pressure.
-
Pipe construction techniques: pipes above-ground and pipes buried.
Unit 3:
Pumps and Compressors Used in Pipelines:
-
Pump interaction with the system, cavitations: work in series and parallel.
-
Multi-pump stations and tanks.
-
Pump calculation and selection.
-
Compressor interaction with the system, avoiding surge, stall, and choking.
-
Multi-compressor stations and gas holders.
-
Compressor calculation and selection.
-
Pipe networks and pipe branching: problems with transients and their control.
Unit 4:
Control Valves in Pipelines:
-
Control valves: selection, sizing, and cavitation issues.
-
Flow measurements and monitoring instrumentation.
-
Pipeline system automation control.
-
Guidelines for pipeline installation, operation, and maintenance.
-
Inspection, examination, and testing of pipelines.
-
The vibration of pipes and pipelines and their mechanical support and anchorage.
Unit 5:
Operation and Maintenance of Piping Systems:
-
Leak detection and prevention and failure risk analysis.
-
Pipeline protection for prevention of corrosion and erosion.
-
Environmental concerns: impact of above-ground and buried pipelines.
-
Off-shore pipelines: design and operation.
-
Special consideration for safety and supervision.
-
Pipeline feasibility study and economic analysis: capital and operation costs.