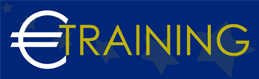

Preventive and Predictive Maintenance
Overview:
Introduction:
Preventive and predictive maintenance refer to institutional systems used to maintain equipment readiness and support operational continuity through structured scheduling and diagnostic frameworks. Preventive maintenance operates through predefined intervals, while predictive maintenance functions based on condition-monitoring indicators and system based evaluations. This training program presents conceptual models, classification systems, and coordination structures that define preventive and predictive maintenance within organizational environments.
Program Objectives
By the end of this program, participants will be able to:
-
Identify structural differences between preventive and predictive maintenance approaches.
-
Outline planning frameworks and institutional logic in preventive maintenance.
-
Classify diagnostic systems and condition indicators in predictive maintenance.
-
Explore models used for interpreting equipment performance data.
-
Evaluate governance structures supporting consistency in maintenance oversight.
Targeted Audience:
-
Maintenance Engineers and Coordinators.
-
Asset Management and Reliability Personnel.
-
Industrial Operations Supervisors.
-
Equipment Lifecycle Planners.
-
Technical Documentation and Oversight Staff.
Program Outline:
Unit 1:
Institutional Structure of Maintenance Systems:
-
Conceptual definitions of preventive and predictive maintenance.
-
Classification criteria of maintenance systems within operational frameworks.
-
Logical distinctions between time based and condition based maintenance.
-
Structural roles of maintenance systems in asset longevity.
-
Maintenance as a component of institutional continuity frameworks.
Unit 2:
Preventive Maintenance Planning and Scheduling:
-
Frameworks for organizing fixed interval maintenance plans.
-
Categorization of equipment by scheduling priority.
-
Documentation structures for recording maintenance intervals.
-
Classification of standard maintenance tasks by system type.
-
Indicators used for assessing schedule alignment with equipment class.
Unit 3:
Predictive Maintenance Logic and System Models:
-
Types of predictive maintenance systems based on diagnostic categories.
-
Role of sensor derived variables in condition classification.
-
Structures for organizing condition thresholds and alert levels.
-
The significant role of the conceptual use of monitoring logic in asset evaluation.
-
Institutional alignment between predictive systems and reliability policies.
Unit 4:
Maintenance Data Interpretation and Forecast Models:
-
Documentation standards for organizing condition data.
-
Models used to classify performance deviation trends.
-
Logical structures for identifying failure probabilities.
-
Linkage between forecast indicators and equipment categories.
-
Role of structured data in maintenance review processes.
Unit 5:
Oversight and Maintenance Governance Structures:
-
Key criteria used to evaluate maintenance system reliability.
-
Governance roles for maintenance policy standardization.
-
Internal structures for compliance review and record validation.
-
Models for tracking performance consistency across equipment classes.
-
Importance of maintenance integration into organizational risk frameworks.