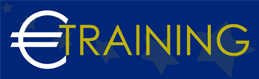

Advanced Maintenance Optimization and Reliability Strategies
Overview:
Introduction:
This training program is designed to provide participants with the required level of technical knowledge and skill to achieve personal satisfaction. Through it, participants will be able to critically analyze the methodologies employed within the organization and instigate improvements where required.
Program Objectives:
At the end of this program, participants will be able to:
-
Understand the Maintenance optimization best practice techniques.
-
Understand a range of equipment failures and their implications to the operational organization.
-
Design a maintenance plan for the upkeep and maintenance inspections of static and rotating plant.
-
Learn a practical approach to developing an action plan to utilize these technologies in their areas of responsibility, fitting them into the overall maintenance strategy, and measuring benefits.
-
Integrate the Reliability Centred Maintenance (RCM), Total Productive Maintenance (TPM), and Condition Based Maintenance (CBM).
Targeted Audience:
-
Maintenance Supervisors and Superintendents.
-
Reliability Engineers.
-
Operational Professionals who are interested in maintenance reliability and asset management.
-
Safety and Integrity Professionals.
-
Professionals involved in process improvement.
Program Outlines:
Unit 1:
Failure of Machines and Inspection Based Failure Analysis:
-
Cavitation in Pumps.
-
Tripping of Turbines.
-
Surging in Compressors.
-
Wear Mechanisms: Fatigue, Fretting, and Corrosion.
-
Fundamentals of Maintenance and Asset Management.
Unit 2:
Failure Analysis and Reliability:
-
Elementary Statistics and Standards.
-
Reliability Models.
-
Learning from Major Failures Case Studies in Process Industries.
-
Learning from Major Failures Case Studies in Oil and Gas Industries.
-
Root Cause Analysis and Extractions of Specific and Generic Lessons.
-
Reflection on Why Systems Fail.
Unit 3:
Statistical Failure Analysis and Reliability:
-
Further Reliability Definitions and Standards.
-
Examples of the Planning Process.
-
Hazard Function and Bath Tub Curve.
-
Weibull Analysis.
-
Rotating Equipment.
-
Major Failures in other Industries.
Unit 4:
Condition Based Maintenance:
-
General Purpose CBM.
-
The P-F Curve.
-
Principles of Vibration Monitoring.
-
Thermal Monitoring.
-
Acoustic Emission.
-
Lubricant Monitoring.
Unit 5:
Decision Analysis in Asset Management:
-
Main Criticism of Existing Management of Computerised Maintenance Systems.
-
The Asset Management Framework.
-
The Decision-Making Grid Approaches.
-
Selection of Appropriate Maintenance Strategies.
-
Integration of RCM, TPM and CBM Approaches.