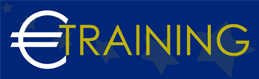

Leadership and Management
TQM and TOC
Overview:
Introduction:
The TQM and TOC training program equips participants with essential skills in Total Quality Management (TQM) and the Theory of Constraints (TOC) for enhanced business performance. Through this program, participants learn to drive continuous improvement and identify constraints to optimize organizational processes.
Program Objectives:
At the end of this program, the participants will be able to:
-
Understand the evolution of quality management in products and services, assess the quality performance of a business and its financial considerations, and recommend an appropriate quality improvement methodology with respect to a company’s structure, culture, and values.
-
Understand the quality management functions, how they are linked, and make recommendations to an organization, while also focusing management effort and resources to best effect.
-
Understand the link between quality, human resources, change management, and leadership, and adapt Lean systems to manage unexpected disruptions.
-
Improve system performance without incurring additional capital or operating costs, and learn how to improve throughput and cycle time without the need for added resources.
-
Increase in inventory turnover and shorten lead times.
Targeted Audience:
-
Managers and leaders seeking to enhance their understanding of Total Quality Management (TQM) and Theory of Constraints (TOC) principles.
-
Professionals involved in process improvement initiatives within their organizations.
-
Employees interested in implementing TQM and TOC methodologies to optimize business processes and enhance organizational performance.
Program Outlines:
Unit 1:
Introduction to Total Quality Management Concepts:
-
Definition of quality and quality models.
-
History of quality.
-
Defining TQM.
-
TQM critical success factors.
-
The relationship between ISO 9000 and TQM.
-
Benefits of implementing a quality model.
Unit 2:
The Success Elements of TQM:
-
Customer-driven quality.
-
Plan, Do Check, Act (PDCA) model.
-
Eight-step problem-solving methodology.
-
Process thinking.
-
Eliminating the non-value added.
-
Management by facts and data.
Unit 3:
Improvement Tools and Methodologies:
-
What is a quality tool?
-
The seven quality control tools.
-
Cause and effect diagram, check sheet, control charts, histogram, Pareto chart, scatter diagram, stratification.
-
Brainstorming.
-
Tree diagrams: how-how and why-why diagrams.
-
Force field analysis.
Unit 4:
Benchmarking As a Tool to Improve Quality and Business Processes:
-
Definition of benchmarking and reasons to benchmark.
-
Levels of benchmarking.
-
Pros and cons of different benchmarking approaches.
Unit 5:
Elements of a Continuous Improvement Process:
-
The eight steps to achieve improvement.
-
Critical success factors and common failure factors in TQM.