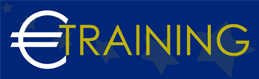

Quality and Operational Auditing
TQM and Continuous Improvement Implementation
Overview:
Introduction:
This training program is designed to equip professionals with the knowledge and skills needed to implement Total Quality Management (TQM) principles and drive continuous improvement within their organizations. It empowers them to drive organizational excellence and achieve continuous improvement goals.
Program Objectives:
At the end of this program, participants will be able to:
-
Understand the principles and practices of Total Quality Management (TQM).
-
Apply TQM tools and techniques to drive continuous improvement.
-
Foster a culture of innovation and excellence within their organizations.
-
Develop and implement TQM strategies to enhance organizational performance.
-
Sustain TQM initiatives and drive ongoing improvement and innovation.
Targeted Audience:
-
Quality managers and improvement leaders.
-
Operations managers and supervisors.
-
Cross-functional teams involved in process improvement initiatives.
-
Individuals seeking to enhance their knowledge of TQM and continuous improvement methodologies.
-
Organizations committed to fostering a culture of quality and excellence.
Program Outlines:
Unit 1:
Introduction to Total Quality Management (TQM):
-
Overview of Total Quality Management (TQM) philosophy and principles.
-
Historical development and evolution of TQM concepts.
-
Understanding customer focus and the importance of meeting customer needs.
-
Key components of TQM, including leadership commitment, employee involvement, and continuous improvement.
-
Comparison of TQM with traditional management approaches.
Unit 2:
TQM Tools and Techniques:
-
Introduction to quality tools commonly used in TQM initiatives.
-
Utilizing tools such as Pareto charts, cause-and-effect diagrams, and scatter diagrams.
-
Implementing statistical process control (SPC) techniques for process monitoring and improvement.
-
Conducting quality function deployment (QFD) to translate customer requirements into product features.
-
Using Six Sigma methodologies to reduce variation and defects.
Unit 3:
Building a Culture of Continuous Improvement:
-
Understanding the principles of continuous improvement.
-
Creating a supportive organizational culture that embraces change and innovation.
-
Developing systems for capturing and implementing employee suggestions and ideas.
-
Implementing Kaizen events and rapid improvement cycles.
-
Establishing key performance indicators (KPIs) to monitor progress and measure success.
Unit 4:
Implementing TQM in Practice:
-
Developing TQM implementation plans and strategies.
-
Identifying and addressing barriers to TQM adoption.
-
Engaging employees at all levels in the TQM process.
-
Establishing cross-functional teams to drive improvement initiatives.
-
Monitoring and evaluating TQM implementation efforts for effectiveness.
Unit 5:
Sustaining TQM and Continuous Improvement:
-
Establishing systems for ongoing measurement and feedback.
-
Conducting periodic reviews and assessments of TQM initiatives.
-
Recognizing and celebrating successes to maintain momentum.
-
Integrating TQM principles into organizational policies and practices.
-
Continuously seeking opportunities for further improvement and innovation.