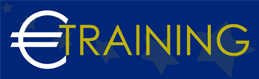

Leadership and Management
Simplification of Work Processes and Procedures
Overview:
Introduction:
This training program is designed to deepen participants' understanding of process design and organizational simplification techniques. It enriches their knowledge, empowering them to apply effective process improvements in their organizations.
Program Objectives:
By the end of this program, participants will be able to:
-
Understand the fundamentals of organizational design and its relationship to complexity.
-
Assess the influence of complex policies on organizational structure and functionality.
-
Apply flow charts and workflow methods to streamline operations.
-
Effectively manage and allocate work among team members within an organizational unit.
-
Evaluate the role of office layout and procedural efficiency in enhancing productivity.
Target Audience:
-
Managers.
-
Supervisors.
-
Employees engaged in procedure design or simplification.
-
End users.
Program Outline:
Unit 1:
The Management Process in Perspective:
-
Key management functions and their effect on processes and procedures.
-
Planning types and frameworks.
-
Structuring and resource allocation strategies.
-
Directing and overseeing individual and team performance.
-
The principles and types of control in management.
-
Essentials of organization design principles.
Unit 2:
Policies and Procedures:
-
Core concepts and definitions.
-
The significance and objectives of procedures.
-
Indicators of overly complex procedures.
-
Goals and benefits of work simplification.
-
Steps to creating effective procedural guidelines.
-
Definition and factors affecting productivity.
Unit 3:
Mapping and Simplifying Processes and Procedures: Tools and Techniques:
-
Improvement methodologies and criteria for procedure selection.
-
Data analysis for procedural enhancements.
-
Identifying and implementing improvement suggestions.
-
Various types of process and procedure mapping.
-
Lean principles for process efficiency.
-
The eight forms of waste and the 5S workplace organization method.
-
Tools like swim lane charts, ESSA methodology, value stream mapping, SIPOC analysis.
-
Process audit techniques, including the turtle diagram and flowcharting.
Unit 4:
Skills Utilization and Workload Distribution Chart:
-
Analyzing with the multi-column process chart.
-
Recognizing skills as the "8th Lean Waste."
-
Creating and assessing Work Distribution Charts (WDC).
-
Redistributing tasks and workload allocation.
-
The impact of industry 4.0 and innovation on process management.
Unit 5:
Simplifying Space Design and Layout:
-
Using spaghetti diagrams for layout and distance analysis.
-
Analyzing and optimizing office/department layouts.
-
Redesigning spaces with office layout charts.
-
Essential size and layout guidelines.
-
Key success factors for effective procedural simplification.