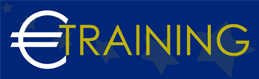

Quality and Operational Auditing
Quality Management ISO 9001 Lead Implementer
Overview:
Introduction:
This program is designed to prepare participants for the certification exam only.
This training program provides participants with comprehensive knowledge and practical skills to effectively implement and maintain ISO 9001 quality management systems. Through it, they are equipped to lead successful ISO 9001 implementation initiatives, ensuring adherence to quality standards and enhancing organizational performance.
Program Objectives:
At the end of this program, participants will be able to:
-
Describe the core ideas and tenets of a quality management system (QMS) based on ISO 9001.
-
From the implementer's vantage point, interpret the requirements of ISO 9001 for a QMS.
-
Utilizing the PECB's IMS2 Methodology and other best practices, begin and plan the implementation of a QMS based on ISO 9001.
-
Assist a company in running, keeping up, and consistently enhancing a QMS based on ISO 9001
-
Prepare for successful completion for the Certification Exam.
Targeted Audience
-
Personnel in charge of preserving and enhancing the caliber of the organization's goods and services.
-
Personnel in charge of satisfying client needs.
-
Consultants, advisors, and other professionals that want to learn more about the standards of ISO 9001 for a QMS.
-
Professionals interested in learning about the PECB's IMS2 Methodology for putting in place a QMS.
-
Those in charge of ensuring that the QMS adheres to ISO 9001 requirements.
-
Members of the operation and implementation teams for the QMS.
Program Outline:
Unit 1:
Introduction to ISO 9001 and the initiation of a QMS implementation:
-
Overview of the ISO, management systems, and ISO 9000 series.
-
Overview of quality and QMS based on ISO 9001.
-
Launching the installation of the QMS.
-
Commitment and leadership.
-
High standards.
-
Attributions, mandates, and powers.
Unit 2:
Implementation plan of a QMS:
-
Setting of the business.
-
QMS range.
-
Taking steps to address opportunities and dangers.
-
Exemplary goals.
-
Change administration.
-
Resources.
-
Competence.
Unit 3:
Implementation of a QMS:
-
Consciousness and dialogue.
-
The control of written information.
-
Product and service requirements.
-
The creation of new goods and services.
-
Outsourcing.
-
Service delivery and production.
-
Evaluation, analysis, and measurement.
Unit 4:
QMS monitoring, continual improvement:
-
Internal audit.
-
Management reviews.
-
Nonconformities and corrective actions.
-
Continual improvement.
Unit 5:
Certification Audit and Closing Procedures:
-
Preparation for ISO 9001 certification audit.
-
Conducting internal audits and management reviews.
-
Addressing nonconformities and implementing corrective actions.
Note: This program is designed to prepare participants for the certification exam only.