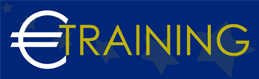

Quality and Operational Auditing
Quality Assurance and Control
Overview:
Introduction:
This training program is designed to equip professionals with the knowledge and skills necessary to ensure the quality and reliability of products and services.It empowers them to drive excellence and customer satisfaction within their organizations.
Program Objectives:
At the end of this program, participants will be able to:
-
Understand the principles and practices of quality assurance and control.
-
Develop and implement effective quality management systems.
-
Utilize quality tools and techniques to improve processes and products.
-
Conduct quality audits and ensure compliance with standards and regulations.
-
Drive continuous improvement initiatives to enhance organizational performance.
Targeted Audience:
-
Quality assurance professionals and managers.
-
Manufacturing and production supervisors.
-
Quality control technicians and inspectors.
-
Regulatory compliance officers.
-
Individuals seeking to enhance their understanding of quality management principles.
Program Outlines:
Unit 1:
Introduction to Quality Assurance and Control:
-
Overview of quality management principles and practices.
-
Importance of quality assurance and control in various industries.
-
Understanding customer requirements and expectations.
-
Role of quality assurance and control in product and service delivery.
-
Introduction to quality standards and regulatory requirements (e.g., ISO 9001).
Unit 2:
Quality Planning and Documentation:
-
Developing quality plans and quality management systems (QMS).
-
Documenting quality policies, procedures, and work instructions.
-
Setting quality objectives and establishing performance metrics.
-
Conducting risk assessments and identifying process improvement opportunities.
-
Ensuring compliance with relevant quality standards and regulations.
Unit 3:
Quality Control Tools and Techniques:
-
Overview of quality control methodologies (e.g., PDCA, Six Sigma).
-
Utilizing statistical process control (SPC) techniques.
-
Implementing process mapping and flowcharting for quality improvement.
-
Performing root cause analysis and corrective/preventive action (CAPA).
-
Using quality tools such as Pareto charts, Ishikawa diagrams, and control charts.
Unit 4:
Quality Auditing and Compliance:
-
Conducting internal and external quality audits.
-
Understanding audit principles and techniques.
-
Evaluating conformance to quality standards and regulations.
-
Developing audit plans and checklists.
-
Reporting audit findings and recommending corrective actions.
Unit 5:
Continuous Improvement and Quality Management Systems:
-
Implementing continuous improvement methodologies (e.g., Lean, Kaizen).
-
Establishing a culture of quality and excellence within an organization.
-
Monitoring and measuring quality performance.
-
Implementing feedback loops and process improvements.
-
Integrating quality management systems with organizational goals and objectives.