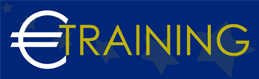

Oil and Gas Technology
Production Facilities Control Room Operation
Overview:
Introduction:
Managing production facilities control room operations involves overseeing the systems and processes that ensure smooth, safe, and efficient production activities, while continuously monitoring equipment and responding to operational changes in real-time. This training program provides participants with comprehensive knowledge and skills for operating control rooms in production facilities. It equips them with the expertise needed to ensure smooth and efficient operation of production processes while maintaining safety standards.
Program Objectives:
At the end of this program, participants will be able to:
-
Analyze and anticipate the behavior of main control loop structures (DCS and SIS systems architecture and functionalities),
-
Explain production equipment, process operating parameters, and perform troubleshooting,
-
Implement proactive, anticipatory control room operation and acquire a safety mindset,
-
React and act in a structured manner to anomalies and plant upsets,
-
Enforce safety guidelines during downgraded and critical situations.
Target Audience:
-
Operators in production facilities.
-
Control room supervisors.
-
Maintenance technicians.
-
Process engineers.
-
Plant managers.
Program Outlines:
Unit 1:
Getting Started - DCS Functionalities for Proper Analysis:
-
Familiarization with HMI functions and operations.
-
Review of DCS tools.
-
Control loop structures: cascade, split-range on the simulator.
-
Introduction to programmable logic controllers and automated sequences.
-
Monitoring start-up sequence (compressor) through MMI.
-
Description of Safety Instrumented Systems (SIS): PSS, ESD, HIPPS, and F&G systems.
Unit 2:
Wells & Production Lines Operation:
-
Well start-up (ramp-up) and shutdown.
-
Analysis of automatic gas control.
-
How to monmitor and detect abnormal conditions in wells.
-
Operation of rotating machinery: centrifugal pumps and compressors.
-
Review of technology, process lines, protection systems, and operating parameters.
Unit 3:
Process Upset Management:
-
Management of alarms: priorities and decision making.
-
Anticipation vs. on-alarm action.
-
Utilization of trend views to predict process disturbances.
-
How to implement routine checks roadmap for global plant performance checks.
Unit 4:
Safety in Operation:
-
Techniques for operating the plant in critical situations and making adequate decisions.
-
How to handle gas leakage, inhibition, and downgraded situations.
-
Steps of ESD activation following leakage detection.
Unit 5:
Production Start-Up:
-
Analysis of production facilities start-up philosophy.
-
Safe plant start-up procedures.
-
Implementation of start-up procedure on the simulator.
-
Anticipation of process upsets and handling malfunctions.
-
The importance of weekly continuous assessment tests on the simulator.