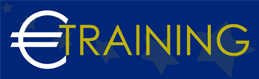

Process Plant Troubleshooting and Engineering Problem Solving
Overview:
Introduction:
This training program aims to equip participants with essential skills and methodologies to effectively diagnose and resolve issues in process plants. This program emphasizes critical thinking, systematic problem-solving approaches, and practical troubleshooting techniques essential for ensuring operational efficiency and reliability.
Program Objectives:
By the end of this program, participants will be able to:
-
Develop proficiency in diagnosing process plant issues.
-
Acquire systematic problem-solving skills.
-
Apply root cause analysis techniques effectively.
-
Implement preventive and corrective actions.
-
Enhance operational reliability and efficiency.
-
Foster a culture of continuous improvement in troubleshooting.
Target Audience:
-
Process engineers and plant operators.
-
Maintenance and reliability professionals.
-
Technical staff involved in operations and troubleshooting.
-
Engineering managers and supervisors.
-
Professionals seeking to enhance problem-solving capabilities in process industries.
Program Outline:
Unit 1:
Fundamentals of Process Plant Troubleshooting:
-
Introduction to process plant troubleshooting.
-
Importance of systematic problem-solving.
-
Roles and responsibilities in troubleshooting.
-
Safety considerations in troubleshooting activities.
-
Regulatory compliance and standards.
Unit 2:
Root Cause Analysis Techniques:
-
Overview of root cause analysis (RCA).
-
Common RCA methodologies (5 Whys, Fishbone Diagram).
-
Data collection and analysis for RCA.
-
Case studies on successful RCA applications.
-
Implementing preventive measures based on RCA findings.
Unit 3:
Equipment and Process Troubleshooting:
-
Troubleshooting mechanical equipment failures.
-
Electrical and instrumentation troubleshooting.
-
Troubleshooting control systems and PLCs.
-
Process deviations and abnormal operations.
-
Interpreting equipment performance data.
Unit 4:
Implementing Effective Solutions:
-
Developing action plans for corrective actions.
-
Monitoring and evaluating effectiveness of solutions.
-
Documenting troubleshooting processes and outcomes.
-
Integration of troubleshooting with maintenance strategies.
-
Continuous improvement in troubleshooting practices.
Unit 5:
Case Studies and Practical Applications:
-
Real-world case studies in process plant troubleshooting.
-
Simulation exercises and hands-on problem-solving.
-
Group discussions and peer learning sessions.
-
Lessons learned and best practices in troubleshooting.
-
Future trends in process plant troubleshooting and problem-solving techniques.