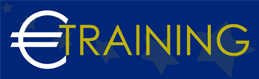

Process Plant Start up and Commissioning
Overview:
Introduction:
This training program prepares participants to oversee the successful start-up and commissioning of process plants. Emphasizing systematic approaches, best practices, and safety protocols, this program empowers them to manage complexities effectively, enhancing plant reliability and operational performance.
Program Objectives:
By the end of this program, participants will be able to:
-
Understand the fundamental phases and principles of process plant start-up and commissioning.
-
Implement systematic approaches and best practices for pre-commissioning and commissioning activities.
-
Apply safety protocols, risk management strategies, and operational readiness assessments during start-up phases.
-
Optimize plant reliability, minimize downtime, and enhance operational performance.
-
Foster effective teamwork and leadership skills essential for successful plant start-up and commissioning.
Program Outlines:
Unit 1:
Fundamentals of Process Plant Start-up:
-
Introduction to Process Plant Start-up: Objectives and Phases.
-
Planning and Preparation: Safety Precautions, Risk Assessment, and Operational Readiness Reviews (ORR).
-
Regulatory Compliance and Permitting.
-
Roles and Responsibilities of Start-up Teams.
-
Documentation Requirements for Start-up Procedures.
Unit 2:
Pre-commissioning and Mechanical Completion:
-
Overview of Pre-commissioning Tasks and Checklists.
-
Mechanical Completion and Integrity Checks.
-
Piping and Instrumentation Checks (P&ID Verification).
-
Equipment and System Inspections.
-
Readiness Criteria for Mechanical Completion.
Unit 3:
Commissioning Procedures:
-
Commissioning Plans and Procedures.
-
System Functional Testing and Validation.
-
Instrument Calibration and Performance Checks.
-
Start-up of Process Equipment and Systems.
-
Verification of Operating Limits and Conditions.
Unit 4:
Operational Readiness and Handover:
-
Operational Handover and Transition.
-
Training and Competency Development.
-
Documentation, Record Keeping, and Reporting.
-
Post-Commissioning Monitoring and Support.
-
Evaluation of Operational Readiness Criteria.
Unit 5:
Continuous Improvement and Safety:
-
Lessons Learned and Continuous Improvement.
-
Safety Reviews and Emergency Response Planning.
-
Long-term Operational Planning and Optimization.
-
Maintenance Planning and Reliability Strategies.
-
Integration of Feedback for Process Enhancement.