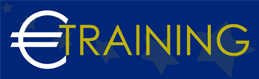

Oil and Gas Technology
Petrochemical and Petroleum Damage Mechanisms API 571
Overview:
Introducion:
This program is designed to prepare participants for the certification exam only.
This training program refers to the identification, understanding, and management of various damage mechanisms that affect equipment and materials in the petrochemical and petroleum industries. API 571 provides guidelines for recognizing types of corrosion, cracking, and material degradation caused by factors such as high temperatures, chemical reactions, and environmental conditions.This training program provides a comprehensive understanding of deterioration processes prevalent in the petrochemical and petroleum industries. Through it, participants will gain valuable knowledge and skills essential for maintaining safe and efficient operations within these industries.
Program Objectives:
At the end of this program, participants will be able to:
- Gain comprehensive knowledge of all 66 damage mechanisms outlined in API 571 Recommended Practices, along with various corrosion and cracking mechanisms.
-
Develop the ability to differentiate and assess the type, extent, and severity of damage mechanisms encountered in plant facilities.
-
Acquire predictive skills to anticipate equipment susceptible to specific damage mechanisms under various design and operating conditions.
-
Explore effective inspection techniques for detecting and preventing well-known damage mechanisms.
-
Prepare thoroughly for the API 571 exam, equipped with the necessary knowledge and skills to attain the API 571 Inspector certificate.
Targeted Audience:
-
Asset Integrity Engineers.
-
NDT Engineers & Technicians.
-
Mechanical Engineers.
-
In service inspector.
-
Professionals who aim to register for API 571 exam.
Program Outline:
Unit 1:
Mechanical and Metallurgical Failure Mechanisms:
-
Introduction to API 571 Damage Mechanisms & Corrosion Basics.
-
Overview of various failure mechanisms such as graphitization, temper embrittlement, and brittle fracture.
-
Explanation of stress-related failures including creep, stress rupture, and thermal fatigue.
-
Identification of specific issues like steam blanketing, DMW cracking, and thermal shock.
-
Understanding erosion, cavitation, and mechanical fatigue in relation to failure mechanisms.
-
Discussion on gaseous oxygen-enhanced ignition and combustion.
Unit 2:
Mechanical and Metallurgical (Continued) & Uniform or Localized Loss of Thickness:
-
Continued exploration of failure mechanisms including refractory degradation and reheat cracking.
-
Steps for Examination of corrosion phenomena like galvanic corrosion, atmospheric corrosion, and CUI.
-
Overview of corrosion in specific environments such as cooling water, boiler water condensate, and CO2.
-
Discussion on corrosion-related issues like flue-gas dew-point corrosion and microbiologically induced corrosion.
-
Explanation of high-temperature corrosion mechanisms like oxidation, sulfidation, and carburization.
-
Understanding corrosion phenomena such as metal dusting, fuel ash corrosion, and nitriding.
Unit 3:
Uniform or Localized Loss of Thickness (Continued) & High Temperature Corrosion:
-
Further exploration of corrosion phenomena including soil corrosion, caustic corrosion, and dealloying.
-
Steps for Examination of specific corrosion types such as graphitic corrosion and oxidation.
-
Overview of environmental-assisted cracking mechanisms including chloride stress corrosion cracking and corrosion fatigue.
-
Discussion on stress corrosion cracking phenomena such as caustic stress corrosion cracking and ammonia stress corrosion cracking.
-
Understanding issues related to liquid metal embrittlement, hydrogen embrittlement, and ethanol stress corrosion cracking.
-
Explanation of sulfate stress corrosion cracking and carbonate stress corrosion cracking.
Unit 4:
Environmental Assisted Cracking and Corrosion Phenomena:
-
Overview of various corrosion phenomena, including amine, ammonium bisulfide, hydrochloric acid, sulfuric acid, and aqueous organic acid corrosion.
-
Examination of specific corrosion types, such as hydrofluoric acid corrosion, high-temperature H2/H2S corrosion, and carbonate stress corrosion cracking.
-
Discussion on localized corrosion issues, including naphthenic acid, phenol, phosphate, and chloride stress corrosion.
-
Explanation of stress corrosion cracking mechanisms, including polythionic acid, amine stress corrosion cracking, and hydrogen stress cracking related to HF.
-
Exploration of unique corrosion phenomena, such as wet H2S damage, alkali corrosion, and acidic corrosion.
-
Understanding the steps for evaluating and managing corrosion phenomena in various operational environments.
Unit 5:
Certification Exam Preparation:
-
Overview of the Certification Exam Structure.
-
Key Topics and Areas of Focus for the Exam.
-
Sample Questions and their Potential Answers.
-
Resources and Materials for Effective Exam Preparation.