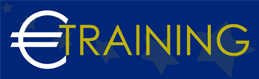

Quality and Operational Auditing
Operational Excellence Managing Performance
Overview:
Introduction:
This training program equips participants with the tools and strategies to achieve operational excellence within their organizations. It empowers them to transform their roles and drive organizational success beyond what traditional training can offer.
Program Objectives:
At the end of this program, participants will be able to:
-
Understand the core principles of operational excellence (OpEx).
-
Identify and eliminate the eight wastes within a process (overproduction, waiting, transportation).
-
Apply lean manufacturing and Six Sigma methodologies to improve efficiency and quality.
-
Utilize data analysis tools to identify performance gaps and opportunities for improvement.
-
Develop and implement performance measurement systems to track progress towards OpEx goals.
-
Foster a culture of continuous improvement within their teams.
Targeted Audience:
-
Operations Managers.
-
Process Improvement Specialists.
-
Quality Control Personnel.
-
Production Team Leaders.
-
Personnel involved in optimizing organizational performance.
Program Outline:
Unit 1:
Foundations of Operational Excellence:
-
Define operational excellence and its key benefits.
-
Explore the eight wastes and their impact on performance.
-
Understand the role of lean manufacturing principles in process optimization.
-
Discuss the core concepts of Six Sigma methodology for defect reduction.
-
Identify the link between OpEx and customer satisfaction.
Unit 2:
Process Analysis and Improvement Tools:
-
Apply process mapping techniques to visualize and analyze workflow.
-
Utilize value stream mapping to identify non-value-adding activities.
-
Implement problem-solving tools like 5 Whys and root cause analysis (RCA) to address performance issues.
-
Explore Kaizen – the concept of continuous improvement – and its practical application.
-
Learn to develop and implement standard operating procedures (SOPs) for consistent performance.
Unit 3:
Data-Driven Performance Management:
-
Understand the importance of data collection and analysis in OpEx initiatives.
-
Utilize various data analysis tools and techniques ( Pareto charts, control charts).
-
Identify key performance indicators (KPIs) to track progress towards OpEx goals.
-
Develop dashboards and reports for effective performance communication.
-
Utilize data analysis to identify trends and predict potential performance issues.
Unit 4:
Implementing and Sustaining Operational Excellence:
-
Develop an OpEx implementation plan aligned with organizational objectives.
-
Learn strategies for overcoming common challenges in OpEx implementation.
-
Implement change management practices to ensure workforce buy-in and adoption.
-
Build a culture of continuous improvement through employee engagement and training.
-
Conduct periodic reviews and audits to assess program effectiveness and identify improvement areas.
Unit 5:
Advanced OpEx Techniques:
-
Explore advanced process improvement methodologies ( Kanban, Poka-Yoke).
-
Introduce the concept of Total Productive Maintenance (TPM) and its role in OpEx.
-
Discuss the integration of OpEx with other management frameworks ( Six Sigma, Balanced Scorecard).
-
Learn how to leverage technology ( automation, data analytics) to support OpEx initiatives.
-
Explore best practices for benchmarking performance against industry leaders.