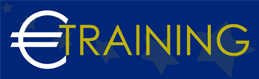

Public Courses
Euro Training's primary focus is on learning and development planning rather than matching participants against a set of criteria. Our practical and interactive approach to courses follows the case study methodology and focuses on clear learning and skills development to meet the ever changing demands of business professionals.
All public courses at Euro Training can be designed and delivered exclusively for a client organisation, or alternatively we can create Customised Training solutions for clients wanting a comprehensive, bespoke training programme. To view a selection of courses that can be customised by Euro Training, click here..
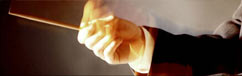
Management & Leadership
Leadership courses integrate strategic methodologies and practical applications that lead organisations to success.
Read more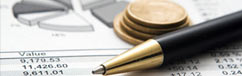
Finance and Accounting Seminars
Finance courses provide the tools and techniques to develop financial strategies, business planning and budgetary control..
Read more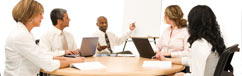
HRM ,Training Seminar
Human Resources Management Courses: HRM Course, Human Capital Course and HR Workshop Human Resources Management Course (HRM Course)
Read more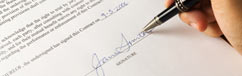
Project, Contract & Procurement
Supply Management Contract Writing Purchasing Seminars and Supply Chain ... Professional Purchasing Project Management Purchasing Seminars
Read more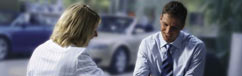
PR & Customer Service
Good communication/customer service skills.Public Relations Consultant, The Media Relations Maven conducts media relations and public relations training, workshops and seminars for a business.
Read more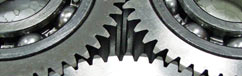
Engineering, Oil and Gas
Petroleum Industry Training Course & Seminar - Oil & Gas Exploration, Drilling, and Completion Fluids, Drilling Fluid Engineering, Drilling Rig Maintenance.
Read more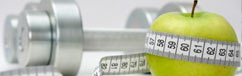
Health, Safety & Security
First Aid Training, Fire Safety Courses, Health & Safety, Security Training Provider. Quality Training.
Read more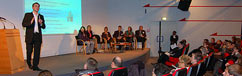
Conferences
Euro Training sponsors more than 900 annual conferences and meetings worldwide. Euro Training is also highly involved in the technical program development of numerous.
Read more