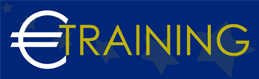

Conferences
Conference on Inventory and Stock Control Management
Overview:
Introduction:
This conference focuses on best practices in inventory and stock control management, emphasizing techniques for optimizing inventory levels, reducing costs, and improving operational efficiency. Participants will gain insights into modern inventory management systems, demand forecasting, and strategies to streamline stock control processes.
Conference Objectives:
By the end of this conference, participants will be able to:
-
Implement efficient inventory control systems to minimize stock issues.
-
Develop demand forecasting techniques to improve inventory accuracy.
-
Apply best practices for managing stock levels and reducing excess inventory.
-
Analyze inventory data for strategic decision-making and cost reduction.
-
Optimize inventory processes to enhance overall operational performance.
Target Audience:
-
Inventory and Stock Managers.
-
Supply Chain and Operations Professionals.
-
Warehouse Managers.
-
Procurement and Purchasing Specialists.
-
Business Owners and Executives involved in stock control.
Program Outline:
Unit 1:
Fundamentals of Inventory Management:
-
Overview of inventory management and stock control principles.
-
Types of inventory: raw materials, work-in-progress (WIP), finished goods.
-
Understanding inventory cycles and their impact on business operations.
-
Key performance indicators (KPIs) for inventory control.
-
The role of inventory management in operational efficiency and cost control.
Unit 2:
Inventory Control Systems and Techniques:
-
Implementing inventory management systems (IMS) and ERP solutions.
-
Stock tracking methods: perpetual vs. periodic systems.
-
Techniques for managing safety stock and reorder points.
-
ABC analysis for categorizing inventory based on value and importance.
-
Strategies for automating inventory processes to reduce errors.
Unit 3:
Demand Forecasting and Inventory Planning:
-
Understanding the importance of accurate demand forecasting.
-
Methods for forecasting demand: historical data analysis, moving averages, and seasonal trends.
-
Integrating demand planning with inventory management for optimal stock levels.
-
Collaborative planning with suppliers and customers to improve forecasting accuracy.
-
Techniques for managing lead times and aligning inventory with market demand.
Unit 4:
Stock Control Optimization and Cost Management:
-
Techniques for reducing excess and obsolete inventory.
-
Managing inventory turnover rates for optimal stock movement.
-
Analyzing inventory costs: carrying costs, ordering costs, and stockout costs.
-
Implementing just-in-time (JIT) inventory management to minimize waste.
-
Best practices for maintaining optimal inventory levels and controlling costs.
Unit 5:
Performance Monitoring and Continuous Improvement in Inventory Management:
-
Setting up performance monitoring systems for inventory control.
-
Regular audits and stocktaking procedures to ensure accuracy.
-
Analyzing inventory data for continuous improvement opportunities.
-
Best practices for managing inventory during business growth or contraction.