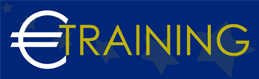

Energy Transition
Comprehensive Guide to Heat Exchangers
Overview:
Introduction:
This training program provides an in-depth presentation of the main types of industrial heat exchangers, their key features and aspects, and provides practical guidelines for selecting the appropriate type for specific applications. Participants will better understand how to use the applicable API, TEMA, and ASME codes, standards, and recommended practices.
Program Objectives:
At the end of this program, the participants will be able to:
-
Highlight the pivotal function and significance of heat exchangers in cost-effective plant operations.
-
Provide a clear understanding of the fundamentals of heat transfer and hydraulics and fluid flow and their application in the thermal design of heat exchangers.
-
Provide methodologies for the mechanical design of heat exchangers following the industry codes, standards, and best practices, specifically ASME BPVC Section VIII, TEMA, and API 660, 661, and 662.
-
Understand the cost-effective technologies and best practices for improving the performance of heat exchangers.
-
Gain essential and integrated knowledge about the hydraulic, thermal, and mechanical design of heat exchangers.
-
Understand, predict and identify causes of performance degradation and damage mechanisms that affect heat exchangers fitness for continued service and thereby reduce the risk of potential failures and waste of energy.
Targeted Audience:
-
Maintenance Professionals.
-
Inspection Personnel.
-
Process Supervisors.
-
Plant Operators.
-
Plant/Technical Managers.
Program Outlines:
Unit 1:
Types and Application of Heat Exchangers:
-
Overview and fundamentals, including the significance of heat exchange in the petroleum, petrochemical, and process industries.
-
Heat Transfer Fundamentals and Heat Transfer Coefficients, covering the basics of heat transfer and coefficients.
-
Various types of heat exchangers and their applications, such as shell and tube heat exchangers, compact heat exchangers, plate heat exchangers, printed circuit heat exchangers, heat pipes, air-cooled heat exchangers, and regenerative heat exchangers.
-
Detailed exploration of Shell & Tube Heat Exchangers (STHE) and Double Pipes, including TEMA nomenclature, front end head types, shell types, rear-end types, double pipe units, and selection guidelines.
Unit 2:
Thermal and Hydraulic Design of Heat Exchangers:
-
Sizing and Specifying the heat exchanger, considering temperature difference in Shell & Tube Heat Exchangers (STHE) and various flow arrangements according to TEMA standards.
-
Understanding countercurrent, co-current, and cross-current flow arrangements, with comparisons between them.
-
Worked example demonstrating the application of velocity triangles and performance derivation from first principles, including pump performance curves and system curve analysis.
-
Fluid Flow and Pressure Drop considerations, focusing on Shell & Tube heat exchangers, Plate heat exchangers, and general design considerations for condensers and reboilers.
Unit 3:
Mechanical Design of Heat Exchangers:
-
Design and construction codes and best practices, including ASME B&PVC Section VIII, API 660, 661, and 662, and TEMA standards.
-
The basic design of heat exchangers, covering Shell & Tube Heat Exchangers (S&THE), Plate Heat Exchangers (PHE), and Air-Cooled Heat Exchangers (ACHE), with special design considerations.
-
Understanding the impact of service conditions on material selection and considering piping loads on exchanger nozzles.
-
Materials of construction for heat exchangers and the fabrication process involved in their construction.
Unit 4:
Operation and Maintenance of Heat Exchangers:
-
Fouling In Heat Exchangers, including types, mechanisms, and the economic impact on design and operation, as well as mitigation strategies by design and operation.
-
Corrosion and erosion considerations in heat exchangers, alongside inspection methods and troubleshooting techniques.
-
Flow-induced vibration analysis, covering mechanisms, prediction methods, and design procedures to avoid vibration, including baffle selection and specialized exchangers.
-
Cleaning strategies and methods for various types of heat exchangers, including Shell & Tube Heat Exchangers (S&THE), Plate Heat Exchangers (PHE), and Air-Cooled Heat Exchangers (ACHE).
-
Heat Exchanger Repairs, focusing on removal and replacement procedures and cost-effective maintenance strategies.
Unit 5:
Performance Enhancement and Optimization of Heat Exchangers:
-
Heat transfer augmentation techniques, including finned tubes and in-tube enhancements such as tube inserts and sintered coatings.
-
Exploration of alternative enhanced tube bundle designs and specialized baffles like rod baffle, heli baffle, and twisted tube configurations.
-
Pinch technology overview and its role in heat exchanger train optimization for enhanced performance.
-
Heat Integration Basics, covering fundamental principles and strategies for optimizing heat integration within process plants.