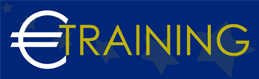

ASQ Approved Lean Six Sigma Green Belt
Overview:
Introduction:
This program is designed to prepare participants for the certification exam only.
This training program is a comprehensive program designed to equip professionals with the skills and knowledge to improve business processes using Lean and Six Sigma methodologies. It empowers them to make data-driven decisions and drive significant organizational improvements.
Programm Objectives:
At the end of this program, participants will be able to:
-
Understand and apply Lean Six Sigma principles and methodologies to various processes.
-
Lead and manage Lean Six Sigma projects using the DMAIC framework.
-
Collect, analyze, and interpret data to identify root causes of process issues.
-
Develop and implement effective solutions to improve process performance.
-
Sustain process improvements through effective control measures and continuous monitoring.
-
Prepare for the certification exam.
Targeted Audience:
-
Mid-level managers looking to enhance their process improvement skills.
-
Quality assurance professionals aiming to implement Lean Six Sigma methodologies.
-
Engineers and project managers seeking to optimize operational efficiencies.
-
Professionals in manufacturing, healthcare, finance, and service industries.
-
Individuals preparing for the ASQ Lean Six Sigma Green Belt certification exam.
Program Outlines:
Unit 1:
Introduction to Lean Six Sigma:
-
Overview of Lean Six Sigma principles and methodologies.
-
History and evolution of Lean and Six Sigma.
-
Key benefits and applications in various industries.
-
Roles and responsibilities in a Lean Six Sigma project.
-
Introduction to DMAIC (Define, Measure, Analyze, Improve, Control) framework.
Unit 2:
Define Phase:
-
Understanding project selection and scope.
-
Defining problem statements and project objectives.
-
Identifying key stakeholders and their requirements.
-
Developing project charters and SIPOC (Supplier, Input, Process, Output, Customer) diagrams.
-
Utilizing voice of the customer (VOC) techniques.
Unit 3:
Measure Phase:
-
Introduction to process mapping and value stream mapping.
-
Identifying and collecting relevant data.
-
Understanding basic statistics and data types.
-
Conducting measurement system analysis (MSA).
-
Calculating baseline performance metrics and process capability.
Unit 4:
Analyze Phase:
-
Performing root cause analysis (RCA) techniques.
-
Utilizing tools like Fishbone diagrams, 5 Whys, and Pareto analysis.
-
Conducting hypothesis testing and statistical analysis.
-
Identifying and prioritizing potential causes of problems.
-
Confirming root causes with data-driven evidence.
Unit 5:
Improve and Control Phases:
-
Developing and selecting improvement solutions.
-
Conducting risk assessments and FMEA (Failure Modes and Effects Analysis).
-
Implementing solutions and managing change.
-
Establishing control plans and standard operating procedures (SOPs).
-
Monitoring results and sustaining improvements with control charts and audits.
-
Preparation for the certified exam.