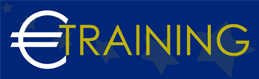

ASQ Approved Lean Six Sigma Green Belt
Overview:
Introduction:
This program is designed to prepare participants for the certification exam only.
This training program provides a comprehensive overview of Lean Six Sigma methodologies, focusing on enhancing process efficiency and reducing waste within various industries. Participants will learn to apply the DMAIC framework to identify, analyze, and address performance gaps effectively. It empowers them to drive sustainable improvements and prepare confidently for Lean Six Sigma certification.
Program Objectives:
At the end of this program, participants will be able to:
-
Grasp core Lean Six Sigma principles and the DMAIC framework to improve processes.
-
Define project goals, identify stakeholders, and develop clear problem statements.
-
Collect and analyze data to identify root causes and performance baselines.
-
Implement targeted improvement solutions and control plans to maintain gains.
-
Prepare effectively for the Lean Six Sigma certification exam.
Targeted Audience:
-
Process Improvement Professionals.
-
Quality Assurance Managers and Specialists.
-
Project Managers seeking efficiency improvements.
-
Operational Managers and Supervisors.
-
Professionals aiming for Lean Six Sigma certification.
-
Team Leaders involved in performance and productivity enhancement initiatives.
Program Outlines:
Unit 1:
Foundations of Lean Six Sigma and the Define Phase:
-
Overview of Lean Six Sigma principles and methodologies.
-
History and evolution of Lean and Six Sigma.
-
Key benefits and applications across industries.
-
Roles and responsibilities in a Lean Six Sigma project.
-
Introduction to the DMAIC (Define, Measure, Analyze, Improve, Control) framework.
-
Understanding project selection, scope, and defining problem statements.
Unit 2:
Defining Project Objectives and Collecting Data (Define & Measure Phases):
-
How to identify key stakeholders and their requirements.
-
Developing project charters and SIPOC diagrams.
-
Utilizing Voice of the Customer (VOC) techniques.
-
Introduction to process mapping and value stream mapping.
-
Identifying and collecting relevant data.
-
Understanding basic statistics and data types for measurement.
Unit 3:
Analyzing Data and Identifying Root Causes (Measure & Analyze Phases):
-
Methods of conducting measurement system analysis (MSA).
-
Calculating baseline performance metrics and process capability.
-
Performing root cause analysis (RCA) with Fishbone diagrams, 5 Whys, and Pareto analysis.
-
Conducting hypothesis testing and statistical analysis.
-
Identifying and prioritizing potential causes of problems.
-
Confirming root causes with data-driven evidence.
Unit 4:
Implementing Solutions and Ensuring Sustainability (Improve & Control Phases):
-
Developing and selecting improvement solutions.
-
Conducting risk assessments and FMEA (Failure Modes and Effects Analysis).
-
Implementing solutions and managing change effectively.
-
Establishing control plans and standard operating procedures (SOPs).
-
Monitoring results and sustaining improvements with control charts and audits.
-
Importance of building a culture of continuous improvement within the organization.
Unit 5:
Exam Preparation:
-
Review of key concepts and skills.
-
Sample exam questions and their potential answers.
-
Exam format and structure overview.
-
Resources for further study and practice.