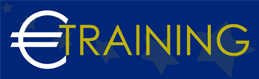

Aspen HYSYS and Process Modeling
Overview:
Introduction:
This training program provides participants with the skills to effectively use Aspen HYSYS software for process simulation and modeling. It enables participants to address real-world engineering challenges and enhance process performance.
Program Objectives:
At the end of this program, participants will be able to:
-
Gain proficiency in building, navigating, and optimizing process simulations using Aspen HYSYS, including advanced steady-state simulations.
-
Utilize various HYSYS functions efficiently to construct comprehensive process flowsheets, leveraging intuitive solving capabilities for rapid model development.
-
Explore multi-flowsheet integration to streamline and organize simulation efforts effectively, using Workbook and Flowsheet interfaces for quick modeling.
-
Enhance convergence characteristics of columns and flowsheets, troubleshoot common issues, and improve simulation accuracy.
-
Utilize Aspen HYSYS's rating capabilities to evaluate the performance of existing equipment and determine optimum operating points through case studies.
-
Learn pipeline hydraulics calculations essential for assessing sizing requirements in gas gathering systems.
-
Discover effective methods for reporting simulation results, including the use of Microsoft Excel VB macros, to communicate findings efficiently.
Targeted Audience:
-
Process Engineers with Process simulation experience.
-
New engineering graduates/technologists who will be using Aspen HYSYS in their daily work.
-
Process engineers doing process design and optimization projects and studies.
-
Plant engineers checking plant performance under different operating conditions.
-
R&D engineers and researchers using Aspen HYSYS for process synthesis.
Program Outlines:
Unit 1:
Propane Refrigeration Loop:
-
Add and connect operations to construct a simple flowsheet.
-
Use the graphic interface to manipulate flowsheet objects and provide a clearer representation of the process.
-
Understand how to process information has propagated both forwards and backward.
-
Convert simulation cases to templates.
-
Build and analyze a propane refrigeration loop simulation.
Unit 2:
Refrigerated Gas Plant:
-
Install and converge heat exchangers.
-
Use logical operations: Adjust and Balance.
-
Model a simplified version of a refrigerated gas plant.
Unit 3:
NGL Fractionation Train:
-
Model distillation columns with the assistance of the Column Input Expert.
-
Manipulate column specifications to better represent process constraints.
-
Evaluate utility requirements using the Process Utility Manager.
-
Model a two-column natural gas liquid (NGL) recovery plant.
Unit 4:
Oil Characterization and HP Separation:
-
Introduce Oil Characterization in Aspen HYSYS.
-
Use the Aspen HYSYS Spreadsheet and Case Study functionality.
-
Use the Oil Environment to characterize a crude assay and then employ the Case Study and Spreadsheet operation to determine how the Gas Oil Ratio (GOR) varies with pressure.
Unit 5:
Gas Gathering System:
-
Simulate a gas gathering system located on varied terrain using the steady-state capabilities of Aspen HYSYS.
-
Use the pipe segment and the Hydraulics subflowsheet to model a piping network in Aspen HYSYS.
Unit 6:
Two-Stage Compression:
-
Introduce the use of the recycling operation.
-
Recognize suitable recycling locations.
-
Implement performance curves for rotating equipment.
-
Utilize the recycle operation to build a two-stage compression flowsheet; define and activate compressor curves.
Unit 7:
Natural Gas Dehydration with TEG:
-
Review the recommended methods to saturate single-phase and two-phase hydrocarbon streams.
-
Discuss the implications of hydrate formation and the different means available to avoid hydrate problems.
-
Model a typical TEG dehydration unit.
-
Model a typical TEG dehydration unit and determine water dew point for the dry gas; use the hydrate utility to investigate the effects of methanol injection on hydrate inhibition.
Unit 8:
Rating Heat Exchangers:
-
Review heat transfer calculation models in Aspen HYSYS.
-
Configure a shell and tube heat exchanger to use a built-in Rating model.
-
Integrate rigorous Exchanger Design and Rating (EDR) calculations into an Aspen HYSYS flowsheet.
-
Use a Rating model to determine if an existing heat exchanger will meet process specifications; design and rate a heat exchanger using the EDR interface inside Aspen HYSYS.
Unit 9:
Troubleshooting / Best Practices:
-
Introduce best practices for product integration and automation.
-
Investigate the reasons why a simulation may produce poor results, consistency errors, etc.
-
Identify appropriate thermodynamic models for common processes.
-
Use suggested tips to debug simulations and columns.
-
Troubleshoot existing Aspen HYSYS cases; recognize common problem areas in an Aspen HYSYS case.
Unit 10:
Reporting in Aspen HYSYS:
-
Create a variety of customized reports using newly added functionality in the Report Manager.
-
Access free Excel utilities designed to extract simulation data.
-
Use Aspen Simulation Workbook to deploy models in Microsoft Excel.
-
Use the Report Manager, Excel utilities, and Aspen Simulation Workbook to obtain custom reports.