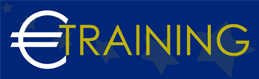

Advanced Process Equipment and Piping Systems
Overview:
Introduction:
Process equipment and piping systems are critical components in industrial operations, playing a key role in transporting, processing, and managing fluids and gases. These systems ensure efficient flow, safe handling, and optimal performance across various industries. This training program combines fundamental knowledge, industry best practices, and practical tools to enhance the competencies of design, operation, and maintenance professionals, ultimately contributing to improved organizational performance, plant safety, and reliability.
Program Objectives:
At the end of this program, participants will be able to:
-
Increase awareness and understanding that mechanical integrity of process equipment and piping systems depends jointly on the proper design, operation, condition assessment, and maintenance of the equipment, underscoring their vital individual and team roles in managing change.
-
Explore practical and sound methods and tools to enable them to carry out basic design calculations for pressure equipment following applicable industrial codes, standards, and best practices.
-
Understand the degradation mechanisms that process equipment could be subjected to over their operating life, how to identify them, predict and determine their impact, and what appropriate measures can be taken to prevent and control the resultant damage.
-
Gain the knowledge and failure analysis skills they need to conduct damage and failure analysis to prevent similar failures from happening.
-
Gain the knowledge and skills of hazard identification and analysis, and in risk assessment and management.
Targeted Audience:
-
Engineers.
-
Technical Professionals.
-
Operations and Maintenance Personnel.
-
Maintenance of Oil & Gas Plants.
-
Oil Refineries & Petrochemical Plants, and Power Plants.
Program Outlines:
Unit 1:
Understanding Process Equipment Failures:
-
Identification of common types of process equipment failures.
-
Analysis of failure mechanisms and root causes.
-
Examination of the consequences of equipment failures on production and safety.
-
Understanding the importance of failure analysis for preventive measures.
-
Failure investigation techniques.
Unit 2:
Failure Prevention Strategies:
-
Implementation of preventive maintenance programs.
-
Utilization of predictive maintenance techniques such as vibration analysis and thermal imaging.
-
Development of equipment inspection schedules and protocols.
-
Incorporation of design improvements for enhanced reliability.
-
Integration of safety systems to mitigate the impact of failures.
Unit 3:
Materials Selection and Compatibility:
-
Understanding the importance of materials selection in equipment design.
-
Examination of material properties and their impact on equipment performance.
-
Evaluation of material compatibility with process fluids and operating conditions.
-
Identification of corrosion and erosion-resistant materials.
-
Consideration of material degradation mechanisms and their prevention.
-
Guidelines for selecting appropriate materials for different process applications.
Unit 4:
Corrosion and Erosion Management:
-
Overview of corrosion and erosion mechanisms in process equipment.
-
Assessment of corrosion and erosion risks in different operating environments.
-
Implementation of corrosion monitoring and inspection programs.
-
Introduction to corrosion-resistant coatings and linings.
-
Application of erosion control measures such as flow optimization and material selection.
Unit 5:
Inspection and Testing Techniques:
-
Introduction to non-destructive testing (NDT) methods for equipment inspection.
-
Visual inspection procedures and techniques.
-
Ultrasonic testing (UT) and radiographic testing (RT).
-
Utilization of magnetic particle testing (MPT) and dye penetrant testing (DPT).
-
Interpretation of inspection results and identification of defects.
Unit 6:
Repair and Rehabilitation Methods:
-
Overview of repair techniques for damaged process equipment and piping systems.
-
Introduction to welding and fabrication methods for equipment repair.
-
Hot tapping and line stopping techniques for in-service repairs.
-
Utilization of composite repair systems for corroded or damaged components.
-
How to rehabilitate corroded pipelines using lining and coating technologies.
Unit 7:
Emergency Response and Contingency Planning:
-
Development of emergency response plans for equipment failures and leaks.
-
Importance of training on emergency shutdown procedures and evacuation protocols on regular bases.
-
Establishment of communication channels and emergency contacts.
-
Effective coordination with emergency response teams and regulatory agencies.
-
How to conduct drills and simulations to test emergency preparedness.
Unit 8:
Regulatory Compliance and Standards:
-
Overview of regulatory requirements and industry standards for process equipment.
-
Understanding of codes and regulations related to pressure vessels and piping systems.
-
Compliance with environmental regulations and emissions standards.
-
Incorporation of safety standards such as API, ASME, and OSHA guidelines.
-
Maintenance of records and documentation for regulatory inspections.
Unit 9:
Reliability Engineering Principles:
-
Introduction to reliability engineering concepts and methodologies.
-
Utilization of reliability-centered maintenance (RCM) strategies for equipment reliability.
-
Application of failure mode and effects analysis (FMEA) for risk assessment.
-
Implementation of reliability modeling and prediction techniques.
-
Integration of reliability engineering into equipment design and maintenance practices.
Unit 10:
Equipment Life Cycle Management:
-
Understanding the life cycle stages of process equipment and piping systems.
-
Analyzing the impact of equipment life cycle on maintenance and operational costs.
-
Establishing criteria for determining the optimal time for equipment replacement or refurbishment.
-
Developing strategies for extending the operational life of equipment through proactive maintenance and design improvements.